What is Squirrel Cage Induction Motor
A squirrel cage induction motor (SCIM) is a type of AC electric motor that uses electromagnetic induction to convert electrical energy into mechanical energy. It’s named for its rotor, which consists of copper or aluminum bars connected by end rings, resembling a squirrel cage. SCIMs are the most common type of industrial motor due to their robust design, reliability, and cost-effectiveness. A Squirrel Cage Induction Motor (SCIM) is a type of asynchronous AC motor.
Types of Squirrel Cage Induction Motors
SCIMs can be broadly categorized based on the number of phases in their power supply:
1. Three-Phase Squirrel Cage Induction Motors
These are the most common type used in industrial applications. They offer high efficiency and power output. Based on their design and performance characteristics, three-phase SCIMs are further classified into several classes (A, B, C, D, E, F) that offer different starting torques, starting currents, and slip characteristics to suit various load requirements. Some key design variations include:
- Standard Design (Class A): Normal starting torque, relatively high starting current, low slip. Suitable for general-purpose applications.
- High Torque, Low Starting Current (Class B): Higher starting torque than Class A, lower starting current, low slip. A common general-purpose motor often replacing Class A.
- High Starting Torque, Normal Starting Current (Class C): High starting torque for heavy loads, normal starting current, low slip. Used for applications like conveyors and crushers.
- High Slip, High Starting Torque (Class D): Very high starting torque, high slip, lower efficiency. Suitable for intermittent loads with high inertia, like punch presses and hoists.
- Low Starting Torque, Low Starting Current (Class E & F): Designed for energy efficiency with lower starting torque and current.
2. Single-Phase Squirrel Cage Induction Motors
These are used in domestic and light commercial applications where only single-phase power is available. Single-phase SCIMs are not self-starting and require auxiliary methods to initiate rotation. Common types include:
-
- Split-Phase Motors: Utilize a starting winding with a resistor or inductor to create a phase difference with the main winding. Disconnected once the motor reaches a certain speed.
- Capacitor-Start Motors: Employ a capacitor in series with the starting winding to create a larger phase difference, resulting in higher starting torque. The starting winding is usually disconnected.
- Capacitor-Run Motors: Have a capacitor permanently connected in series with an auxiliary winding, improving running efficiency and power factor.
- Capacitor-Start, Capacitor-Run Motors: Combine the benefits of both capacitor-start and capacitor-run configurations for high starting torque and efficient running.
- Shaded-Pole Motors: Have a small copper ring (shading coil) around a portion of each pole.The induced current in the shading coil creates a phase difference, producing a weak starting torque. Used in low-power applications like fans.
Motor Components
A squirrel cage induction motor primarily consists of two main parts:
- Stator: The stationary part of the motor. It includes:
-
- Stator Frame: The outer housing that provides mechanical support and protection.
- Stator Core: Made of laminated silicon steel to reduce eddy current losses. It has slots on its inner periphery to house the stator windings.
- Stator Windings: Insulated copper wires wound and placed in the stator slots. When connected to a power supply, these windings create a rotating magnetic field.
- Rotor: The rotating part of the motor. It includes:
-
- Rotor Core: Also made of laminated silicon steel to minimize losses and is mounted on the motor shaft. It has slots on its outer periphery.
- Rotor Cage: Consists of conductive bars (aluminum or copper) embedded in the rotor slots and short-circuited at both ends by metal end rings. This forms a closed electrical circuit.
Other essential components include:
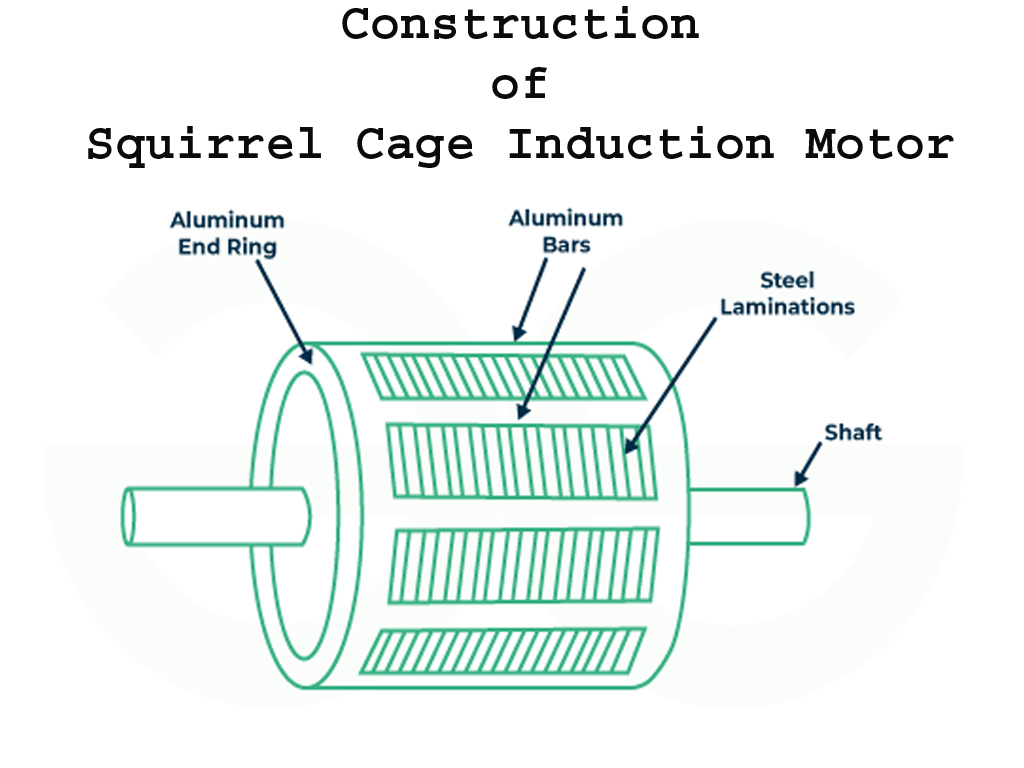
-
- Bearings: Support the rotor shaft and allow it to rotate freely.
- End Shields: Cover the ends of the motor, housing the bearings and providing protection.
- Cooling Fan: Often attached to the rotor shaft to circulate air and cool the motor.
- Terminal Box: Provides a safe connection point for the power supply cables.
Working Principle
The working principle of a squirrel cage induction motor is based on electromagnetic induction and the interaction between magnetic fields:
- Rotating Magnetic Field: When a three-phase AC power supply is connected to the stator windings, it produces a rotating magnetic field (RMF). The speed of this rotating magnetic field is called the synchronous speed () and is determined by the frequency of the supply () and the number of poles () in the stator winding:
- Induced Current in the Rotor: This rotating magnetic field sweeps across the stationary rotor conductors (the bars of the squirrel cage), inducing an electromotive force (EMF) in them according to Faraday’s law of electromagnetic induction. Since the rotor bars are short-circuited by the end rings, this induced EMF causes a current to flow through the rotor conductors.
- Rotor Magnetic Field: The current flowing in the rotor bars creates its own magnetic field around the rotor.
- Torque Production: The interaction between the rotating magnetic field produced by the stator and the magnetic field produced by the rotor current results in a torque on the rotor, causing it to rotate. According to Lenz’s law, the direction of the induced rotor current and its magnetic field is such that it opposes the change that produced it. Therefore, the rotor tries to catch up with the rotating magnetic field.
- Slip: The rotor never quite reaches the synchronous speed of the rotating magnetic field. If it did, there would be no relative motion between the RMF and the rotor conductors, no induced EMF, no rotor current, and hence no torque. The difference between the synchronous speed ( ) and the actual rotor speed ( ) is called slip ( ), usually expressed as a percentage:
Design Variations
Type | Features |
Double Cage Rotor | Two-layer rotor bars; inner for torque, outer for starting performance. |
Deep Bar Rotor | Deep rotor bars to improve starting torque due to skin effect. |
Cast Aluminum Rotor | Lightweight, common for small motors. |
Copper Rotor | Higher efficiency but costlier. |
High Slip Motors | Designed with more rotor resistance for high starting torque needs. |
Applications
Squirrel cage induction motors are widely used in various industrial, commercial, and domestic applications due to their versatility and reliability. Some common applications include:
-
- Industrial Drives: Pumps, fans, blowers, compressors, conveyors, machine tools (lathes, milling machines, drilling machines), printing machinery, flour mills.
- Refrigeration and HVAC: Freezers, air conditioners, refrigerators, ventilation systems.
- Commercial Buildings: Pumps, elevators, escalators, ventilation systems.
- Household Appliances: Washing machines, dryers, dishwashers, vacuum cleaners, mixers, fans, hair dryers.
- Power Generation: In some cases, SCIMs can be used as generators, particularly in wind turbines and hydroelectric power plants, when driven above synchronous speed.
- Material Handling:Cranes, hoists.
- Transportation: Electric vehicles (traction motors in some applications).
Advantages
Squirrel cage induction motors offer several advantages:
-
- Simple and Rugged Construction: Fewer moving parts compared to other motor types, leading to high reliability and long lifespan.
- Low Initial and Maintenance Cost:Simple design makes them relatively inexpensive to manufacture and maintain, as there are no brushes or slip rings to wear out.
- High Efficiency: Generally have good to high efficiency, especially at or near full load.
- Good Speed Regulation: Maintain a relatively constant speed under varying load conditions.
- High Overload Capacity: Can handle temporary overloads without stalling.
- Simple Starting Arrangement: Can be started directly on the line (DOL) for smaller ratings, or with simple starters (star-delta, autotransformer) for larger ratings.
- High Power Factor (at high loads): Operate at a reasonably good power factor when loaded.
- Explosion-Proof: Absence of brushes and commutators eliminates the risk of sparking, making them suitable for hazardous environments.
- Low Rotor Copper Losses: Due to the short-circuited rotor bars.
Disadvantages
Despite their numerous advantages, SCIMs also have some limitations:
-
- Poor Starting Torque (for some designs): Standard designs may have relatively low starting torque compared to their running torque.
- High Starting Current: Can draw a high starting current (5 to 8 times the full-load current), which may cause voltage dips in the power supply and require special starting methods for large motors.
- Limited Speed Control: Speed is primarily determined by the supply frequency and the number of poles, making efficient and wide-range speed control more complex and often requiring variable frequency drives (VFDs).
- Sensitive to Supply Voltage Fluctuations: Performance can be affected by variations in the supply voltage.
- Lower Power Factor at Light Loads: The power factor tends to be low when the motor is lightly loaded.