Definition of Cable
A cable is a collection of one or more conductors, often insulated, that are used to transmit electrical power, signals, or data between two or more points. Cables are widely used in electrical installations, communication networks, and in various industrial, commercial, and residential applications. The conductors in a cable are typically made of copper or aluminum, and the insulation is made from materials like PVC, rubber, or XLPE (cross-linked polyethylene).
Types of Cable Joints
A cable joint is a connection between two or more sections of electrical cables to extend the cable length, repair a damaged cable, or provide a way to link cables of different types or sizes. There are several types of cable joints, and they are selected based on factors such as the type of cable, the voltage level, and the environmental conditions.
Here are the main types of cable joints:
- T-Joint: Used when you need to make a branch connection from a main cable to a secondary cable, forming a “T” shape. Often used in both power distribution and communication networks when branching off a main cable.
T-Joint or T Type cable joint
Joint Procedure:
- First remove the insulation from center of horizontal wire up to length of 5 cm.
- Remove the insulation from ends of second wire up to length of 8 cm.
- Clean the ends of wire with sand papers.
- Place the second wire at 90Ëš angle on the horizontal line and couple them with each other.
- Take 6-7 turns for bending & Sold the join with soldering wire.
- Fit the insulating tape to the joint area. Use heat tools (hot air or heat gun) ensuring it forms a tight, protective seal around the joint.
- Apply a sealing compound to any exposed areas for additional protection against moisture.
- Pigtail joint: A pigtail joint is a type of cable joint used to create a branching connection from a main cable. It involves attaching a short piece of conductor (resembling a “pigtail”) to the main cable, allowing it to connect to another cable or device. This joint is commonly used in low- and medium-voltage wiring systems for simple, cost-effective connections. Proper insulation is essential to ensure safety and prevent electrical faults.
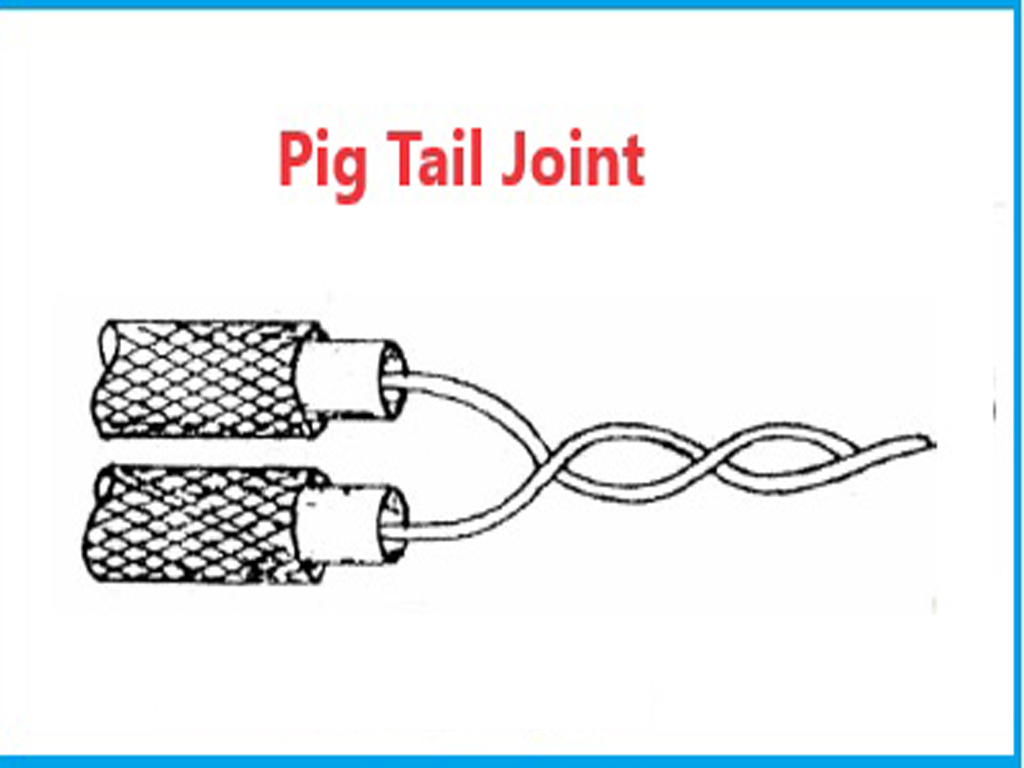
Procedure of pigtail joint:
First remove the insulation from two or more wire end of up to 5 cm and twist them with each other.
- Married joint: A married joint is a type of cable joint where two cables are joined together by twisting or braiding their conductors. This joint is commonly used to make permanent, secure connections in electrical systems. It is typically used for low- and medium-voltage applications and requires proper insulation to ensure safety.
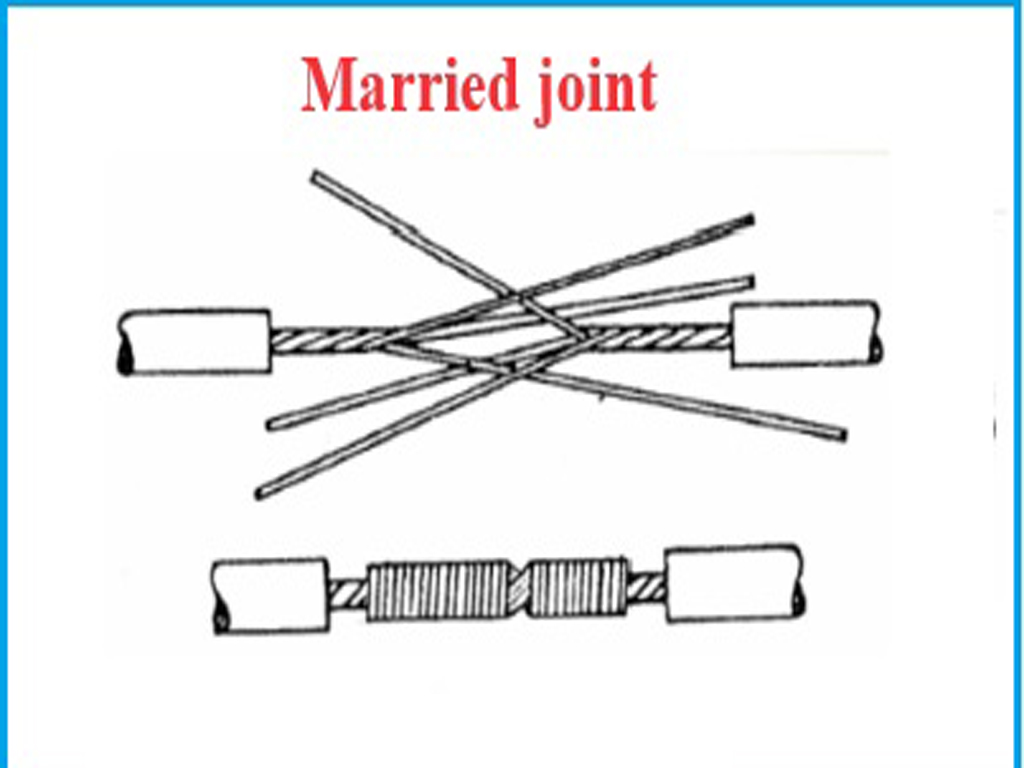
Joint Procedure:
- First remove the insulation from Ends of both wire up to length of 8 cm.
- Clean the ends of wire with sand papers.
- Twist them from insulation Ends of wire up to length of 3 cm.
- Take 6-7 turns for both wire each other.
- Fit the insulating tape to the joint area. Use heat tools (hot air or heat gun) ensuring it forms a tight, protective seal around the joint.
- Apply a sealing compound to any exposed areas for additional protection against moisture.
4. Straight Joint: To join two cables of the same type and size, often to extend the length of the cable. Commonly used in low and medium-voltage applications for connecting cables that are similar in construction.
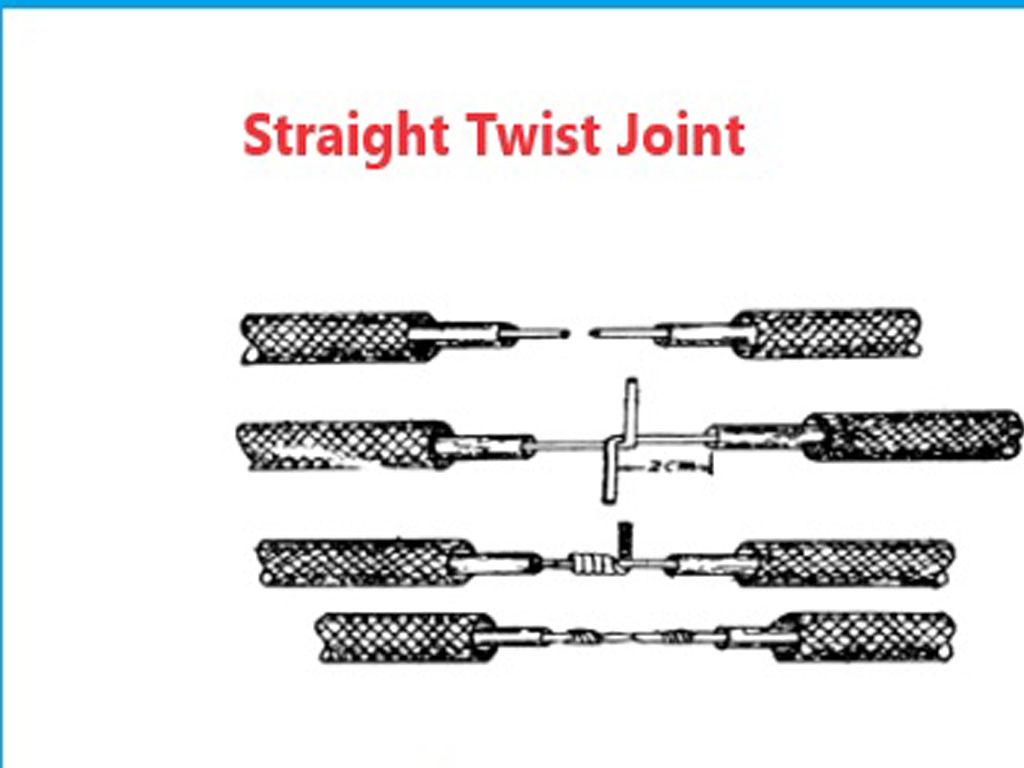
Joint Procedure:
- First remove the insulation from ends of both wires & cables up to minimum length of 8 cm.
- Clean the ends of wire with sand papers.
- Bend the two wires from 2 cm at 90Ëš angle and couple them with each other.
- Take 6-7 turns for bending.
- Fit the heat-shrink tubing or insulating tape to the joint area. Use heat tools (hot air or heat gun) to shrink the tubing, ensuring it forms a tight, protective seal around the joint.
- Apply a sealing compound to any exposed areas for additional protection against moisture.
- Perform an insulation resistance test on the joint to ensure it is properly insulated. Verify the integrity of the joint by checking the continuity and insulation resistance.
- Wrap the joint in protective sheathing if necessary. Ensure everything is properly secured and recheck safety.
- End Joint (Termination Joint): To connect a cable to an electrical device or another cable at the end of a cable run. This joint helps in terminating the cable properly and provides a safe interface between the cable and the equipment. Used in both medium and high-voltage systems for connecting to electrical equipment such as transformers, motors, or switchgear.
- Dead End Joint: Used at the end of a cable run where the cable is not connected to anything, but must be safely sealed off. Common in power cables, especially for protection against short circuits and electrical faults.
- Pot End Joint: Typically used to connect medium and high-voltage cables, especially in underground or outdoor installations. It provides mechanical strength and protection to the joint by using a resin-filled pot, which provides a waterproof and insulating seal.
- Heat Shrink Joint: Uses heat-shrinking materials (such as sleeves or tubes) to seal and insulate the joint area. Common in medium and high-voltage applications due to its reliability and ease of use. This type of joint provides excellent insulation and protection against moisture, dirt, and mechanical stresses.

- Cold Shrink Joint: Involves the use of pre-stretched elastic rubber tubes that shrink onto the joint when released. Often used for making connections in a faster and more efficient manner compared to heat shrink joints. Suitable for both indoor and outdoor environments.
- Britannia joint: A Britannia joint is a type of cable joint used to connect two cables by joining their conductors through a mechanical or compression method. It is commonly used for connecting medium and high-voltage cables and invol
Britannia joint ves the use of copper or aluminum conductors. The Britannia joint provides a secure, low-resistance connection and is typically insulated to prevent electrical faults. It’s known for its reliability in power transmission and distribution systems.
Joint Procedure:
- Gather necessary tools and materials (cable joint kit, insulation, heat-shrink tubes, etc.) & Ensure safety protocols are in place (PPE, de-energizing cable, etc.).
- Cut the cable ends square and remove the outer sheath.
- Strip back the insulation carefully from the cable ends at least 8-10 cm (for both conductors and earth).
- Clean the exposed conductor and check for any damage.
- Insert the cable conductors into the appropriate connector or 6-8 turns for joining.
- Fit the heat-shrink tubing or insulating tape to the joint area. Use heat tools (hot air or heat gun) to shrink the tubing, ensuring it forms a tight, protective seal around the joint.
- Apply a sealing compound to any exposed areas for additional protection against moisture.
- Perform an insulation resistance test on the joint to ensure it is properly insulated. Verify the integrity of the joint by checking the continuity and insulation resistance.
- Wrap the joint in protective sheathing if necessary. Ensure everything is properly secured and recheck safety.
- Duplex (Double Tee) Joint: A Duplex (Double Tee) Joint is a type of cable joint that involves connecting two cables using a specialized technique where both cables are joined in parallel, typically forming a “T” shape or dual connection. This type of joint is used for medium- and high-voltage cables, particularly in situations where two cables need to be spliced or interconnected at a common point. It is called “Duplex” or “Double Tee” because the joint often connects two cables at both ends, making a T-shaped configuration with a central section that interconnects the two cables.
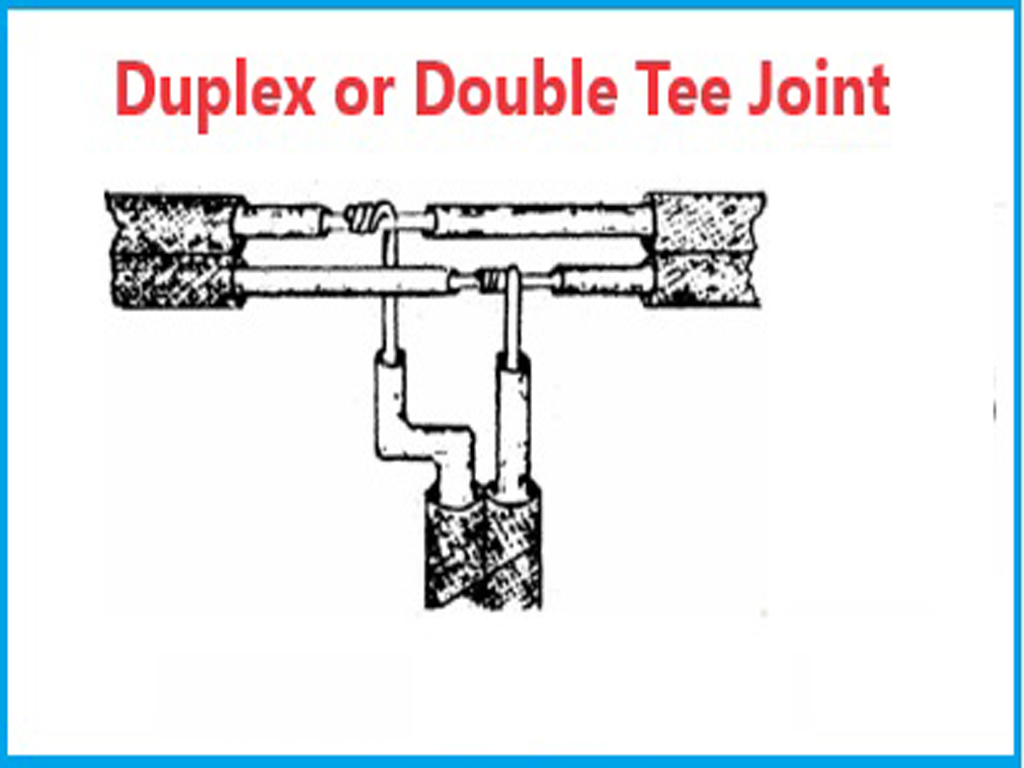
Joint Procedure:
- Strip the insulation: Remove the outer insulation of both cables at the jointing area up to 12cm.
- Clean the conductors: Ensure the conductors are clean and free of any dirt, oxidation, or debris.
- Measure and cut: Ensure the cables are cut to the correct length for the joint and that there is enough length to properly connect them.
- Align the cables: Position the two cables in the correct alignment for the “T” or parallel connection.
- Twist or connect the conductors: For the “T” connection, the conductors of the two cables are usually twisted or connected using compression lugs or connectors or 6-8 turns for joining.
- Secure the connection: Ensure the connection is mechanically secure and has minimal resistance by using proper connectors, clamps, or compression tools.
- Insulate the joint: Once the conductors are properly connected, insulate the joint area using heat-shrink tubing, resin, or other appropriate materials.
- Seal the joint: Ensure the joint is waterproof and protected from environmental conditions by applying additional insulation and sealing materials.
- Test the Joint: After completing the joint, conduct electrical and mechanical tests to ensure the connection is safe, secure, and meets the necessary standards for performance.