Electrical cable jointing kits
Electrical cable jointing kits are essential for connecting two or more electrical cables, extending their length, or repairing damaged sections. They provide insulation, mechanical protection, and environmental sealing to ensure the longevity and safety of the electrical connection. The types of cable jointing kits primarily differ based on the technology used for insulation and sealing.
Heat Shrink Cable Jointing Kits
Heat shrink cable jointing kits are one of the most common and versatile types. They consist of tubes, caps, and breakouts made from cross-linked polymeric materials that shrink radially when heated.
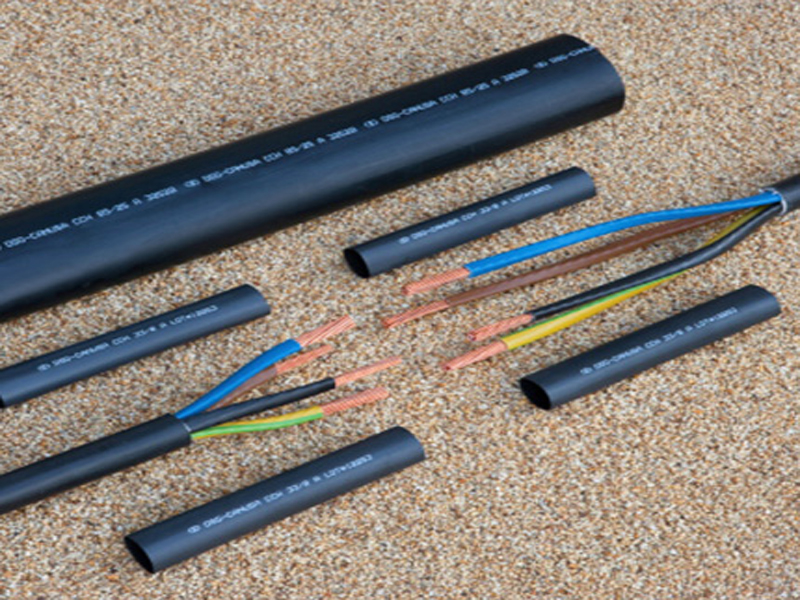
How They Work
Components: Heat shrink tubing, insulating tapes, connectors, mastic, sealing sleeves.
When heat (usually from a gas torch) is applied, the material shrinks tightly around the cable components, forming a secure, waterproof, and insulated seal. The inner surface of many heat shrink products is coated with a thermoplastic adhesive that melts and flows to fill any voids, enhancing the seal and moisture resistance.
Application:
Low, medium, and high voltage cables.
Advantages
- Excellent insulation properties: Provides high dielectric strength.
- Good mechanical protection: Offers resistance to abrasion and impact.
- Environmental sealing: Protects against moisture, chemicals, and UV radiation.
- Versatility: Available for a wide range of cable types and voltages (low, medium, and high voltage).
- Reliability: Proven technology with a long track record.
Disadvantages
- Requires a heat source (torch), which can be inconvenient or hazardous in certain environments.
- Installation requires some skill and training to ensure proper heating and shrinkage.
Cold Shrink Cable Jointing Kits
Cold shrink cable jointing kits offer a flame-free alternative to heat shrink. They are pre-stretched onto a removable plastic core and contract upon removal of the core without the need for heat.
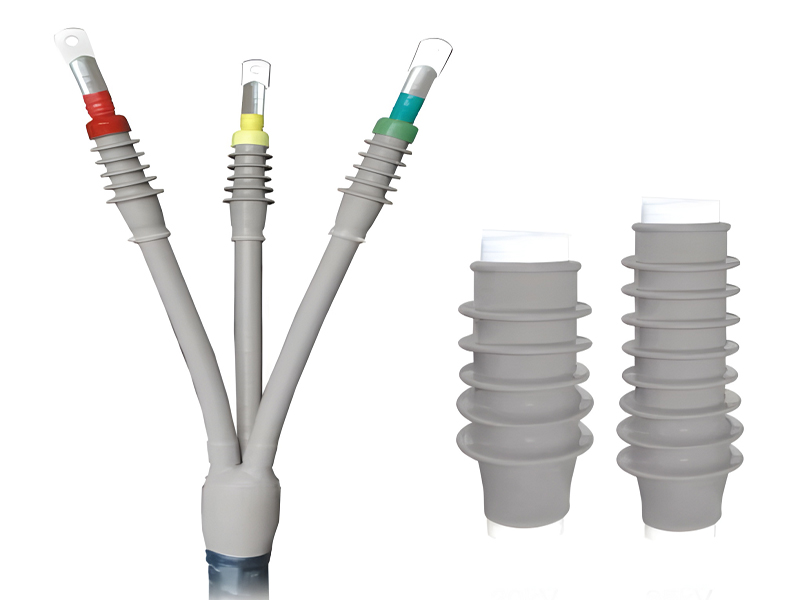
How They Work
Components: Cold shrink tubes, connectors, sealants, stress control tubing.
The jointing components are typically made from silicone rubber or EPDM (ethylene propylene diene monomer) rubber. They are supplied pre-stretched over a rigid, spiral plastic core. Once positioned over the cable joint, the installer simply pulls out the core, allowing the rubber sleeve to uniformly shrink onto the cable, creating a tight seal.
Application:
Medium and high voltage cables.
Advantages
- No heat required: Eliminates the need for torches, making them safer for use in hazardous environments.
- Faster installation: Generally quicker to install than heat shrink kits as there’s no heating time.
- Consistent pressure: Maintains a constant radial pressure on the cable, providing excellent environmental sealing and insulation.
- Resistant to UV and ozone: Silicone rubber is particularly good in outdoor applications.
Disadvantages
- Can be more expensive than heat shrink kits.
- May have less mechanical strength compared to some heat shrink solutions for very heavy-duty applications.
- Limited shelf life due to the pre-stretched state.
Resin (Cast Resin) Cable Jointing Kits
Resin jointing kits use a liquid resin that is poured into a mold around the cable joint, which then hardens to form a solid, insulated, and protected connection.

How They Work
Components: Resin compound, transparent mold shell, connectors, gloves.
The kit typically includes a two-part resin (e.g., polyurethane or epoxy) and a plastic or metal mold. After the cables are connected (e.g., with connectors or crimps), the mold is placed around the joint. The two parts of the resin are mixed and then poured into the mold, encapsulating the entire joint. The resin cures and hardens, providing a rigid, watertight, and highly insulated joint.
Application:
Low and medium voltage.
Advantages
- Excellent moisture barrier: Provides superior waterproofing, making them ideal for direct burial or submerged applications.
- High mechanical strength: The hardened resin offers robust protection against impact and compression.
- Good chemical resistance: Resistant to many chemicals and oils.
- Can fill irregular shapes: The liquid resin conforms to the shape of the joint.
Disadvantages
- Longer curing time: The resin needs time to harden, which can delay commissioning.
- Irreversible: Once the resin cures, the joint is permanent and difficult to reopen for inspection or repair.
- Messy to install: Involves mixing and pouring liquid resin, which can be messy if not handled carefully.
- Temperature sensitive: Curing time can be affected by ambient temperature.
Pre-Molded/Push-On Cable Jointing Kits
Pre-molded or push-on jointing kits consist of factory-molded elastomeric components that are simply pushed onto the prepared cable ends.
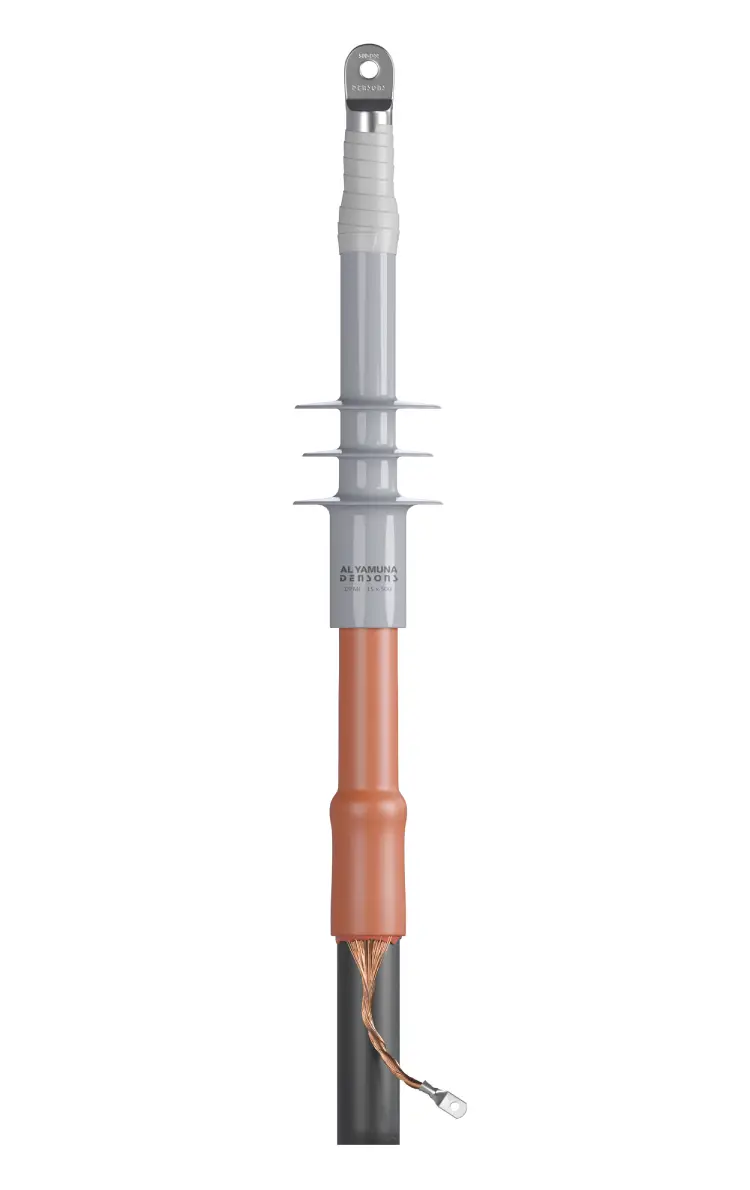
How They Work
Components: Pre-molded joint body, stress cones, connector, sealing system.
These kits typically use EPDM or silicone rubber components that are designed to fit snugly over the cable insulation. They are supplied as pre-engineered pieces that are slid or pushed onto the cable, relying on the inherent elasticity of the material to provide a tight seal and insulation.
Application:
Medium and high voltage cables.
Advantages
- Very fast installation: Requires minimal preparation and no special tools or heat.
- Clean installation: No messy resins or heat.
- Reliable performance: Factory-tested components ensure consistent quality.
- Can be re-enterable: Some designs allow for re-entry for maintenance.
Disadvantages
- Limited flexibility: Each component is designed for specific cable dimensions, making them less adaptable to variations.
- Can be more expensive than other types.
- Less common for low voltage applications compared to medium and high voltage.
5. Straight through Joint Kits
- Application: All voltage levels.
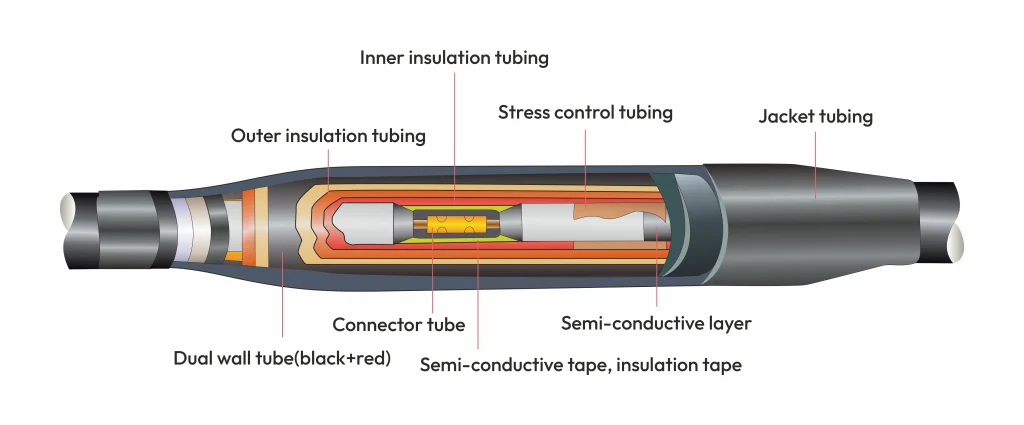
- Features:
- Designed to join two cable ends in a straight line.
- Available in all technologies (heat shrink, cold shrink, resin, etc.).
- Used in: Underground or duct cable installations.
6. Transition Joint Kits
- Application: Connecting different types of cable (e.g., PILC to XLPE).
- Features:
- Specially designed to accommodate the physical and electrical differences.
- Used in retrofits and repairs involving cable upgrades.
Other Specialized Kits
Beyond the primary types, there are specialized kits for specific applications:
- Low Voltage Resin Inline Joints: Often used for street lighting, direct burial, or underground connections where waterproofing is critical.
- Insulated Piercing Connector (IPC) Kits: Used for quick and safe connections in overhead or insulated power lines without stripping the cable insulation.
- Water-Blocking Tape Kits: While not a complete jointing kit, these tapes are often used in conjunction with other methods to enhance water blocking in splice kits.
Choosing the right cable jointing kit depends on various factors, including the cable type, voltage level, environmental conditions (e.g., moisture, temperature, UV exposure), space constraints, installation time, and cost.