Ah, a fascinating project! Integrating a Direct-On-Line (DOL) starter for motor control with a solar power system presents some interesting considerations. Controlling a motor using a Direct-On-Line (DOL) starter from a solar power system involves integrating solar panels, an inverter, and standard motor starting components.
Components Required:
- Solar Panels
- Charge Controller (if using a battery system)
- Battery Bank (optional but recommended for reliability)
- Inverter (DC to AC) – sized to motor voltage and startup current
- Contactor
- Overload Relay: Trips the circuit if current exceeds motor rating
- STOP button: Normally Closed (NC)
- START button: Normally Open (NO)
- Seal-in Contact: Keeps the contactor energized after START is released
- Three-phase Motor
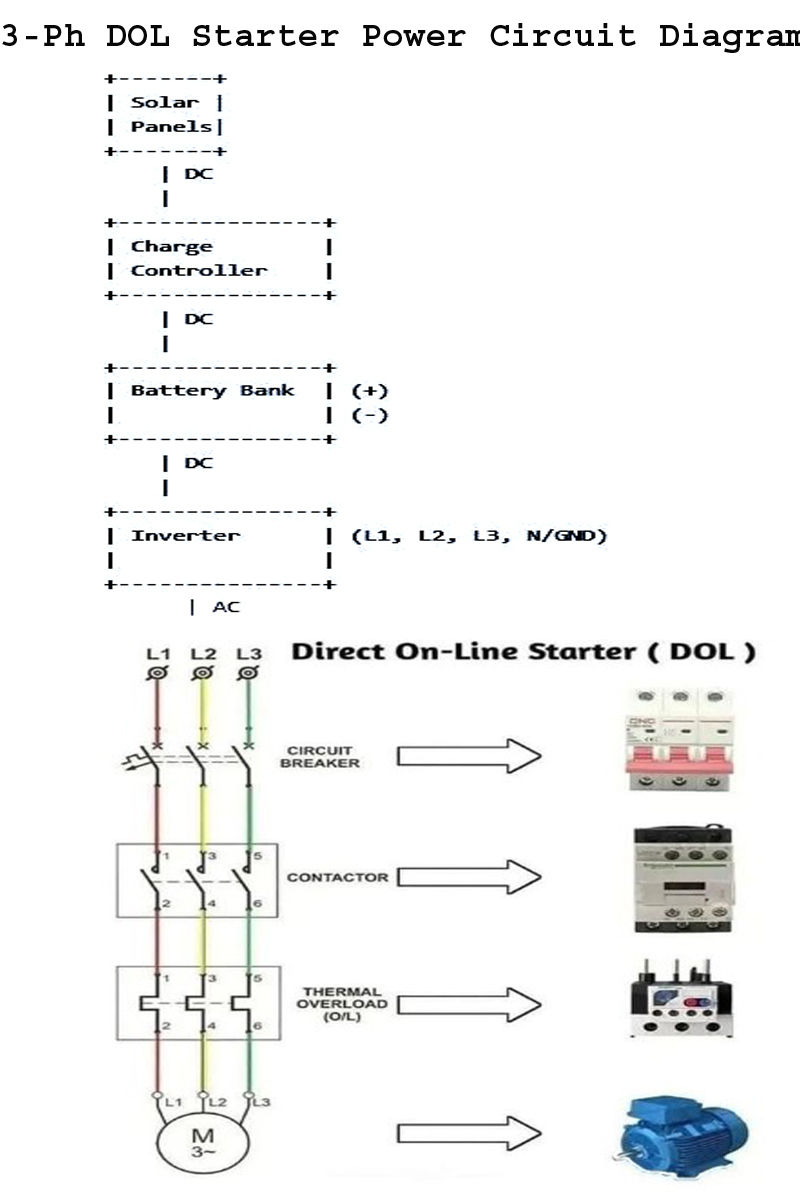
âš¡ Working Principle
- Solar Panels generate DC power.
- Charge Controller manages battery charging (if batteries are used).
- Inverter converts DC to 3-phase AC.
- DOL Starter directly starts the motor by connecting it to full line voltage via contactor.
- Control Circuit includes push buttons to operate the contactor coil, protected by an overload relay.
✅ Important Considerations:
ï‚·Â What kind of motor are you planning to control? (e.g., horsepower, voltage, current requirements)
ï‚·Â What is the size and capacity of your solar system? (e.g., total wattage of panels, battery bank capacity if any, inverter specifications)
ï‚·Â What is the intended application of the motor? (e.g., pumping water, running a small machine, ventilation)
ï‚·Â Protection: Fuse or MCB on the output side of inverter
ï‚·Â Monitoring: Include voltmeter, ammeter, and fault indicator if needed
ï‚·Â Do you need continuous operation or intermittent use?
ï‚·Â Do you have any specific requirements for safety or control features?
However, I can certainly share some general principles and potential challenges involved in such a setup:
General Principles:
- Power Matching: The most crucial aspect is ensuring that your solar system can consistently provide the necessary power to start and run the motor under load. DOL starters draw a high inrush current (typically 6-8 times the full-load current) for a short duration during startup. Your solar system, especially the inverter and any battery bank, must be able to handle this surge without tripping or experiencing a significant voltage drop.
- Inverter Compatibility: The inverter you use must be capable of handling the motor’s starting current. Some inverters have surge current ratings, which indicate their ability to handle temporary overloads. You’ll need to carefully compare the motor’s locked-rotor current (LRC) with the inverter’s surge capacity.
- Battery Bank Considerations (if applicable): If your system includes batteries, their capacity and discharge rate will be critical for supplying the starting current. Deep-cycle batteries are generally recommended for solar applications due to their ability to handle repeated charge and discharge cycles.
- DC to AC Conversion: Solar panels generate DC electricity, which needs to be converted to AC by an inverter to power a standard AC motor and DOL starter. The efficiency of this conversion is also a factor to consider.
- Protection: Just like with a grid-connected motor, you’ll need appropriate protection devices, such as:
- Circuit breakers or fuses: To protect against overcurrents and short circuits on both the DC and AC sides.
- Overload relay: Integrated into the DOL starter to protect the motor from sustained overcurrents.
- Low-voltage protection (LVP) or under-voltage release (UVR): To prevent the motor from restarting automatically after a power interruption (which could happen with fluctuating solar power) and potentially causing damage or safety hazards.
- Wiring and Connections: Proper wiring with adequate gauge is essential to minimize voltage drop and ensure safe operation.
Potential Challenges:
- High Starting Current: The large inrush current of a DOL starter can be a significant challenge for smaller solar systems or inverters with limited surge capacity. This might lead to voltage dips, inverter shutdowns, or premature battery wear.
- Intermittent Solar Power: Fluctuations in sunlight can affect the voltage and current output of the solar panels. This can potentially cause the motor to stall or the DOL starter to trip if the power drops below the required level during operation.
- System Sizing: Accurately sizing the solar system components (panels, inverter, batteries) to reliably handle the motor’s demands, especially the starting current, can be complex and potentially expensive.
- Efficiency Losses: Each stage of the power conversion (DC to AC) introduces some energy loss, which needs to be factored into the overall system design.
Potential Solutions and Considerations:
- Soft Starters or Variable Frequency Drives (VFDs): For larger motors or systems with limited power capacity, consider using a soft starter or a VFD instead of a DOL starter. These devices gradually increase the voltage and frequency supplied to the motor during startup, significantly reducing the inrush current. While they add complexity and cost, they can make motor control feasible with a smaller solar system.
- Larger Inverter with High Surge Capacity: If you stick with a DOL starter, ensure your inverter has a surge rating significantly higher than the motor’s locked-rotor current.
- Adequate Battery Bank: If using batteries, ensure they have sufficient capacity and a high enough discharge rate to handle the starting current without a significant voltage drop.
- Load Management: Implement strategies to avoid starting the motor when other high-power loads are running on the solar system.
- Direct DC Motors: If the application allows, consider using a direct DC motor powered directly from the solar panels (possibly with a DC-DC converter for voltage matching). This eliminates the need for an inverter and the associated losses.
To give you more specific advice tailored to your situation, please provide more details about your motor and solar system. I’m here to help you figure this out!